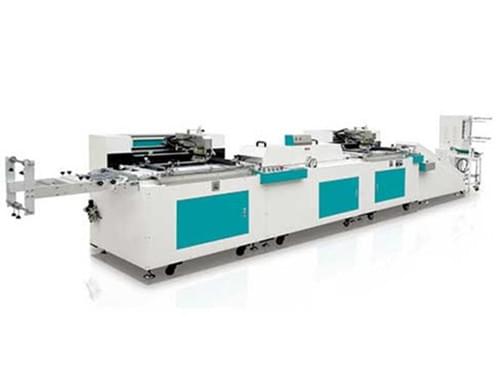
Screen Printing Machine for Elastic Tape – Tough on Stretch, Easy on You
Title: LX-3000G-2C Screen Printing Machine for Elastic Tape – Tough on Stretch, Easy on You
Model: LX-3000G-2C
Valid Printing Area: 28cm x 650cm (big space for long runs)
Max Printing Speed: 750M/h/tape (keeps up with demand)
Max Power: 12KW/70A/380V (strong and steady)
Machine Dimension: 9.6M x 1.0M x 1.3M (fits most shops)
Weight: ~1200KG (built to last)
Applications: Handles elastic tape screen printing machine jobs like elastic cords, textile tapes, cotton tapes, grosgrain, satin ribbons, garment labels, shoelaces, lanyards, and webbing slings with ease.
Need a reliable screen printing machine for elastic tape? The LX-3000G-2C tackles stretchy materials head-on, delivering crisp, multi-color prints fast. Chat with us for details and kickstart your next project!
Worry about the machine's quality and our service? Please see what our clients say , click here.
LX-3000G-2C Screen Printing Machine for Elastic Tape – Master Your Stretchy Prints
Printing on elastic tapes and cords can be a real headache—stretchy materials twist, inks smear, and patterns stretch out of shape if the machine isn’t up to the task. The LX-3000G-2C elastic tape screen printing machine is your fix. Built to handle elastic tapes and elastic cords, this screen printing machine for elastic tape pumps out crisp, vibrant prints that hold up, even when the material pulls and flexes. With a huge printing area and a fast pace, it’s ready to tackle your toughest elastic printing jobs without slowing down.
This elastic cord printer shines where others stumble. Its imported core parts keep it reliable, while the quiet design cuts noise so you can focus. Whether you’re laying down a single-color logo or stacking up to 6 colors on elastic tapes, this machine keeps every detail sharp—no warping, no fading. It’s cost-effective too—big-brand quality without the big-brand price, plus free installation and 24/7 support to keep you rolling. Wondering how to screen print elastic tape? Just load it up, set your design, and watch it deliver—stretchy never looked so good.
For anyone battling elastic printing woes, the LX-3000G-2C screen printing equipment is a game-changer. Perfect for businesses needing fast, flawless prints on elastic cords or tapes, it’s built to last and easy to run. Don’t let stretchy materials trip you up—reach out now for the full scoop on this silk screen printing machine and turn your elastic projects into winners!
Why It Crushes Elastic Printing Challenges:
- Stretch-Savvy: Prints stay put on elastic tapes—no smearing or stretching out.
- Color Control: 1C-6C options for bold, layered designs on elastic cords.
- Noise-Free: Ultrasound enclosure keeps your shop quiet while it works.
- Big Jobs, No Sweat: Massive area and speed for long elastic tape runs.
- Support You Need: Free setup and round-the-clock help—zero stress.
Who It’s Built For:
- Elastic Tape Pros: Fast screen printing machine for elastic tape for bulk orders.
- Cord Printers: Precise elastic cord printer for clean, stretchy results.
- Growing factory: Affordable screen printing equipment that scales with you.
Ready to ace elastic tape printing? Contact us today for LX-3000G-2C details—fast delivery, top-notch prints, and stretch-ready power are waiting!
The advantages of using CNY Printer's elastic tape screen printing machines include:
• Cost-effective compared to major brands
• Same level of performance and quality
• Fast delivery • 24/7 online support
• Assist clients in saving money
You may need the following auxiliary devices for your screen printing solution.
2. Screen plate exposure machine
3. Screen plate constant temperature drying oven
What is the elastic tape?
Elastic tape is a type of stretchy material that is used in a variety of applications, including clothing and textiles, medical and athletic support, and industrial and household repairs. It is made from a variety of elastic fibers, such as rubber, spandex, or a blend of synthetic materials, and is typically used to create flexible and stretchable products or to add stretch and support to existing material.
There are several types of elastic tape, including woven elastic tape, which is made from interwoven elastic fibers, and braided elastic tape, which is made by braiding elastic fibers together. Elastic tape is often used in clothing and textiles to provide a comfortable and flexible fit, and it is also used in medical and athletic support products to provide compression and support to injured or strained muscles.
Elastic tapes are narrow, stretchy ribbons of fabric that are commonly used in clothing, accessories, and other textile products. They are often used to provide stretch and flexibility to fabrics, and to create a snug fit around the body or other objects. Some of the key characteristics of elastic tapes include:
Stretchability: Elastic tapes are designed to stretch and then return to their original shape. This allows them to provide a comfortable, snug fit, and to move with the body as it bends and stretches.
Durability: Elastic tapes are typically made from strong, synthetic fibers that are designed to withstand repeated stretching and wear.
Elastic recovery: Good quality elastic tapes should have a high level of elastic recovery, meaning that they return to their original shape quickly and consistently.
Width and thickness: Elastic tapes can come in a range of widths and thicknesses to suit different applications.
When it comes to printing on elastic tapes, there are a few difficulties that can arise:
Limited surface area: Elastic tapes are typically quite narrow, which can make it difficult to print detailed designs or text.
Stretching: Because elastic tapes are designed to stretch, any printing on them needs to be able to stretch and recover without cracking or fading. This can require specialized inks or printing techniques.
Adhesion: Because elastic tapes are often made from synthetic fibers, it can be difficult to get printing inks or adhesives to adhere properly to the surface of the tape.
Colorfastness: Elastic tapes are often used in clothing and other products that need to be washed regularly. Any printing on the tape needs to be colorfast and able to withstand multiple washings without fading or running.
Frequently asked questions about screen printing inks
Screen printing ink, hence the name, refers to all the inks that are processed using the screen-printing method. When using screen printing ink in the use of sometimes there will be some problems. The following small series is for you to take stock of screen printing ink in the use of common failures and handling methods:
1. FOAMING: Printing viscosity is too high, drying too fast, plate and substrate from too fast, a bad layout, ink itself, and other factors. can take appropriate measures to adjust, or add the appropriate amount of defoamer and replace the ink.
2. Block: due to drying too fast, printing speed being too slow, printing viscosity being too high, the use of poor and improper diluent, printing plate being affected by the wind, ink fineness, or impurities caused by. It should be appropriate to adjust the drying rate or replace the ink.
3. PINHOLE: Because the printing body is too smooth, the printing surface with a grease protective layer or with impurities, the ink itself is not good, so must be printed surface pretreatment, add a leveling agent, or replace good ink.
4. Poor adhesion: due to improper selection of ink, Insufficient pre-treatment; substrate has sundries, drying temperature and time is insufficient; the number of additives, curing agent, and drying agent are not appropriate, two-component ink overprint, the under-color solidifies too hard, and so on, factors cause. Because the chemical polarity of materials such as PE, PP, PET, and aluminum foil is quite low or too smooth, they are generally treated by spark, flame, and strong acid immersion to improve the surface tension of the printing surface. After the ink film of the two-component ink is cured, due to the chemical reaction, the cross-linked ink film becomes dense and strong, and the ink film after complete cure is difficult to corrode by the solvent. Therefore, when superimposing printing, the ground color table can be printed after it is dry, and other factors can be adjusted accordingly.
5. Wire drawing: The reason is a too high viscosity, drying too fast, and ink, resin and solvent caused by improper, should use the right solvent, adjust the appropriate viscosity or replace good ink.
6. Migration, fading: Due to the use of inappropriate ink pigments, especially a large number of plasticizer films, more prone to migration, should choose the appropriate inks.
7. Whitening or printing surface is foggy: Because the diluent contains water, printing ambient air humidity, or printing ink itself is bad. As the printing surface dries, solvent evaporation will absorb heat around, resulting in local water vapor solidification in the ink film inside or surface caused by white atomization, so should choose the appropriate drying rate or reduce space humidity, or replace the excellent ink.