When you want to get a high quality of screen printing result. Firstly, you should buy a good performance silk screen machine ( someone prefers to call this kind of equipment screen printing machines too). Secondly, you have to make sure every step of preparation for your screen printing works is correct. Such as masking film, screen mesh stretch, screen mesh exposure, materials color position alignment, and have good operation experience on automatic silk screen machine.
Process flow of screen printing
Mesh Stretching( fix the mesh cloth on the frame)
- set the screen frame according to a certain angle of tilt, with the mesh stretch machine to clamp the mesh cloth.
- When stretching the mesh, first stretch the diameter line, then the weft line and apply the suitable tension
- Raise the frame so that the cloth is coated with adhesive when it comes to uniform contact with the frame.
- After the adhesive chemicals harden, cut off the mesh frame from the mesh cloth.
Pre-treatment (cleaning the dirt on the yarn)
Washing the yarns with detergent, remove the water, and dry it at 40℃.
The future works will carry out in a dust-free room.
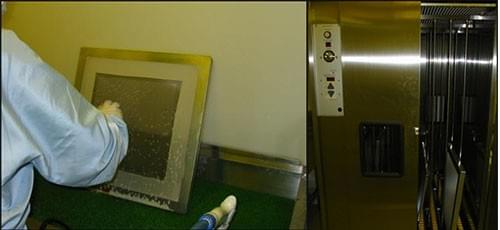
Coating emulsion (surface coating of a photosensitive emulsion)
(1) Put the stretched yarn in contact with one side of the container containing the photosensitive emulsion, evenly coated emulsion. (Repeated coating several times)
(2) Measure the thickness after drying.
(3) To reach the index thickness of the emulsion, repeated steps①②.
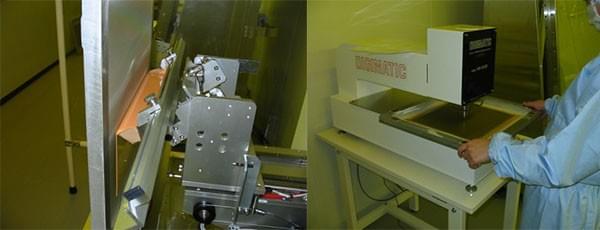
Exposure
(1) Expose the mask tightly to the emulsion surface.
The transparent part of the mask can pass through UV light, hardening the emulsion.
The black area of the mask cannot penetrate the UV light, so the emulsion does not harden.
(2) put it into the exposure machine, with UV light irradiation.
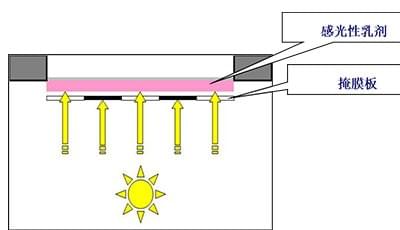
Imaging (remove the unexposed part of the emulsion)
Spray water with a portable ejector. After the unexposed part of the emulsion has expanded, spray air to remove it and dry it after water removal.
Through UV light irradiation, the hardening of the emulsion has left on the yarns. Use water to wash the emulsion that has not been hardened on the screen to form a pattern.
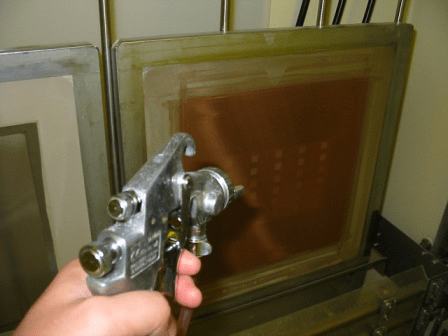
Checking
Using a magnifying glass and measuring machine, check whether the pattern is defective or not.
If you have high accuracy requirements of the screen mesh, after checked by the magnifying glass, you still need to use the quadratic element detector to double inspection. Such as determine the size of the openings, the location of the pattern accuracy.
Measure the thickness and tension of the screen after exposure and drying.
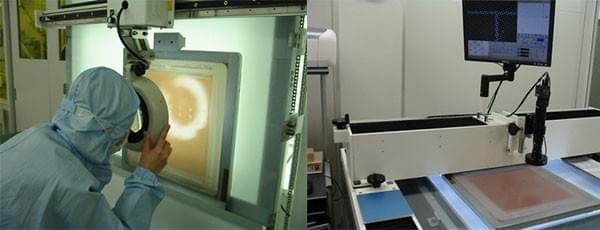
The main function of yarn in screen printing.
(1)The pattern forms the supporting body of the required emulsion
(2)To give the screen printing plate of tension
(3) control substrate film thickness of the partition
(4) control ink penetration
The pattern forms the supporting body of the required emulsion
To ensure the formation of fine line patterns. The photosensitive emulsions must also maintain a very slim and even shape.
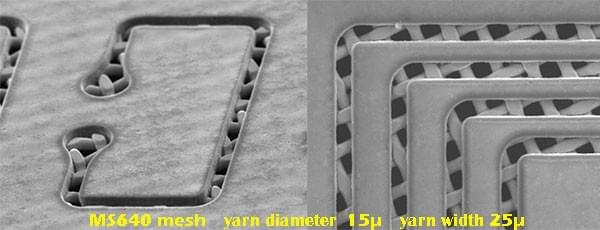
Now used in line width printing of 50 microns, except for 500 mesh products,640mesh, 730mesh, and 840mesh, they are all been productization.
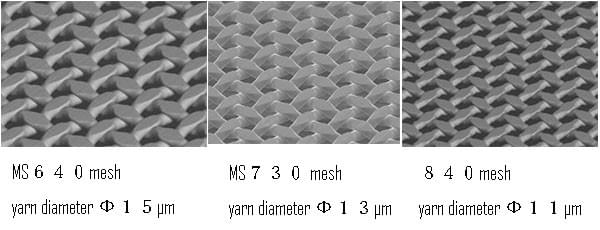
If you are looking for a reliable supplier of screen printer in China, you can back to our website having a look at our automatic screen printing machines.
We are sure our machines quality and after service will not let you down.
Websites: www.iprintingpress.com l www.cnyprinter.com
Contact: Ms Yuki
E-mail: yuki@cnyprinter.com