A simple definition: Plastisol ink is one of the most commonly used screen printing ink type and has been around for decades. It has been the primary ink until fairly recently as more and more companies have been converting. Plastisol is a much more user friendly ink, as it is more accurate for matching Pantone colors.
Screen printing involves the use of plastisol inks. Plastisol inks are easy to use in printing. But they can be hazy on dark materials and stick fast to most fabrics. There are two elements in plastisol ink. Those elements are plasticizer (thick clear liquid) and PVC resin (white powder). They will never cure or dry at room temperatures. For a proper cure, the degrees must be 290 to 330º F
Plastisol inks can go with any surface that can handle the heat. Thanks to the heat are necessary to cure the ink. It is porous enough to allow great penetration of ink. Plastisol inks never color the fabric like a dye. Rather than that, the ink folds over the fibers. Then creates a strong mechanical bond with the fabric. So, they won't stick to non-porous materials like metal, glass, and plastic. They won't stick well to woven and waterproofed nylon fabric without a bonding agent.
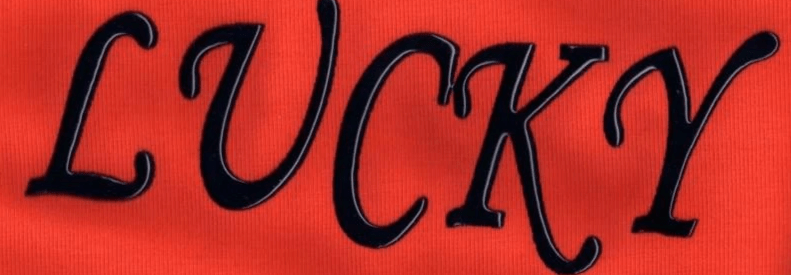
Select the right mesh
There's a big variety of different meshes to select from. Choosing the right one will be a tough decision. For this, you should consider the information mentioned below as a guideline.
- Consider using 30 to 38 mesh for glitter plastisol ink.
- Consider using 60 to 85 mesh for athletic prints.
- Consider using 60 to110 mesh for fleece products.
- Consider using 60 to 85 mesh for puff inks.
- Consider using 60 to 85 mesh for metallic plastisol ink
- Consider using 60 to 85 mesh for bleed-resistant or super opaque:
- Consider using 60 to 85 mesh for hot-split heat transfers:
- Consider using 110 to 125 mesh for general plastisol prints.
- Consider using 180 to 200 mesh for wet-on-wet or multi-color plastisol printing.
- Consider using 180 to 230 mesh for nylon jacket printing.
Select appropriate emulsion
For this, there are a lot of choices out there. You can get the dual-cure emulsion stencils for plastisol inks. It’s intended to use for plastisol inks. For example, Capillary film stencils are likewise a great choice. It becomes an ideal approach when printing halftones and transfers.
Use the right plastisol ink additives
Pay attention when you choose ink additives. It is quite simple to ruin the chemical balance of plastisol inks. You can disbalance it by using the wrong additives or by including too much of the right additive. Then you will get the outcome of a print that doesn't cure. It becomes an issue that you won't notice until someone washes a shirt and the design comes out. Select the additives after reading the technical datasheets for each additive and ink. Then do follow their guidelines, because it's an easy way to avoid the problems.
Don't include mineral spirits to plastisol ink. Even though with mineral spirits it becomes easy to print at first. But soon the ink will become harder and even stiffer to use than before. There's also a possibility that mineral spirits start preventing the ink from curing.
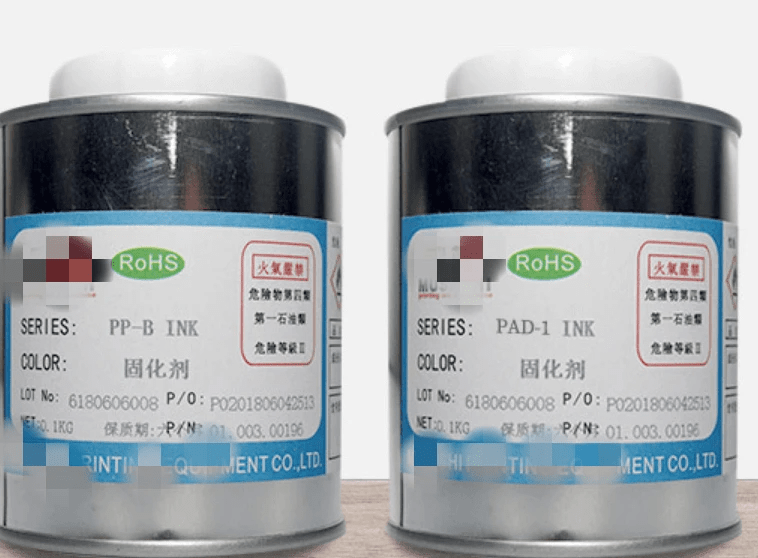
Store the ink
Store plastisol inks at the right temperature that implies room temperature. The degree should be above 90º F. Because it permits the ink to start curing even when it’s still in the container.
Wash screen frame
Clean your screens by removing plastisol ink off. You can clean it by using mineral spirits or any one of the different brands of screen washes that you can get from your screen-printing supplier.
Control dye migration
Dyes migration is an issue caused by dyes. Especially in polyester fibers transferring or changing the colors of plastisol inks. The common colors use to migrate are maroon, green, red, or a few of the darker blue tones. Dye migration occurs faster after the quick curation of the ink. But it might take hours, days, or even two weeks. To control dye migration, you need to follow the procedures mentioned below:
- Print with high-opacity and use low-bleed inks.
- Don't use a higher temperature than the actual printing needs to cure the ink. Using more heat is one of the major reasons for dye migration.
- Print a low-bleed white under the base. At that point, print the required color tone over that.
- Stay away from this issue by printing on pure cotton stuff or fabric.
Print washability
The washability of cured direct or transfer prints should be better. Dry cleaning is not preferred. Never use the iron on the printed spot of the garment.
Cure Plastisol Inks
Curing plastisol inks is a process of exposing them by using the proper temperature. Even if within the right duration of the time. The correct curing of plastisol ink is quite important. The most common issue occurs from the poor washability of plastisol ink. Almost in every case, this happens because of the incomplete ink cure.
When the plastisol heats, the resin elements absorb the liquid (plasticizer) and swell. Then they start mixing and make a hard-elastic film. It is not possible to over cure direct prints. Because the over cure temperature is higher than the heating point of the stuff. Although to heat the ink layer above than 350º F don't recommend. Because when you close the drying oven then puff inks will fall like a cake. Then there will be even more issues with dyes migration. When the thickness of the ink doesn't set to the right curing temperature, the ink will be under-cured. It means that the resin has not consumed all the plasticizers, and the ink will come off the stuff if washed.
Measure ink temperature
The use of test strips is critical for finding temperatures of the printed ink film. For the evaluation of thick prints, you should place the tap inside the materials. Because you need to make sure the right temperature sets at the ink film's bottom. Temperature tools and pyrometers (infrared thermometers) can be useful likewise. Because they are very precise at measuring temperature. But if you don't properly use these tools, they might show wrong temperature readings of the ink film. Due to these tools might not react enough details to temperature changes in the ink film.
Measure the time
When the ink film thickness sets to the proper temperature, the ink is completely cured. It implies that the high temperature in the curing unit can cure the plastisol even in a few seconds.
Adjust your dryer
It’s significant to know the adjustments of your dryer to get the right curing temperature. There is a common misconception that you should measure the temperature of the dryer. Instead, you should only need to find the temperature of the ink film.
By measuring the time of the heating process, you can find the temperature of the ink film. You can likewise set the heater's temperature. It indicates that you can control the temperature by using the dryer's belt speed. Also, you can control the time under the heater by using a flash curing unit. When the heater temperature is 800º F, you can get the complete cure temperature in a few seconds. The degrees in the dryer is set higher than the temperature needed to cure the ink. It permits the ink to cure faster for improving the printing speed.
Final Words
Plastisol inks are harmless when you use it with sensible consideration. Pure plastisol ink doesn't involve volatile organic compounds or air-polluting solvents. The production, storage, disposal, and transportation of plastisol inks won't cause environmental contamination. As long as you follow the right environmental protection and safety instructions.