This comprehensive guide covers the core classifications, technologies, materials, and terminology related to flexographic printing plates in 2023. For both experienced flexo printers and those new to the process, understanding the distinctions between plate types and capabilities is essential for determining the optimal plates for any printing objective.
Photosensitivity Classifications
Photosensitivity, or the reactivity to light exposure, divides flexo plates into two main categories:
Rubber Plates:
- Made from natural and synthetic rubber materials.
- Do not rely on photosensitive chemicals to create the image.
- Limitations include potential issues with dimensional stability.
- Suited for short-run jobs on coated substrates.
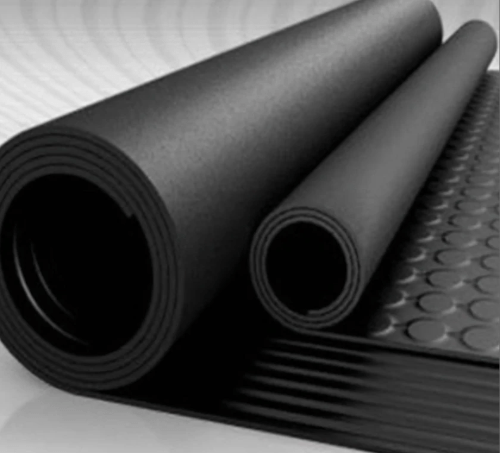
Photosensitive Resin Plates:
- Use photopolymer resins that harden when exposed to light.
- Two sub-types exist:
- Solid Photosensitive Resin - uniform solid sheet construction.
- Liquid Photosensitive Resin - relies on liquid-type resins.
- Offer high resolution and print consistency across long-run jobs.
- Leading photopolymer plate manufacturers include DuPont, MacDermid, Asahi.
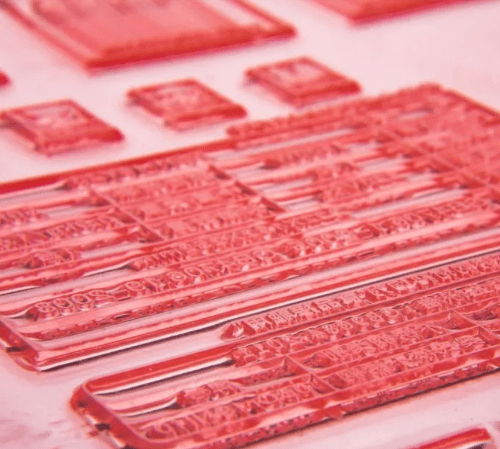
Platemaking Process Classifications
Flexo plates can be categorized into three major types based on plate-making technology:
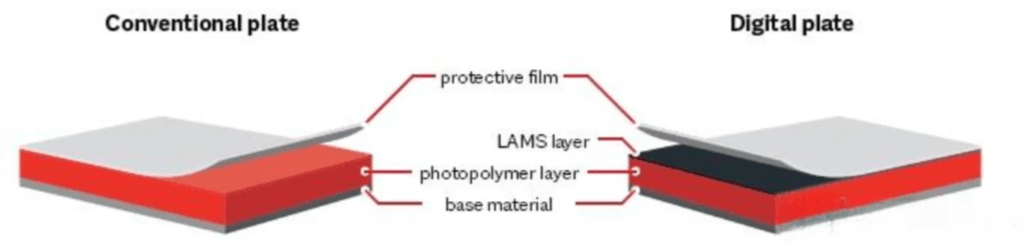
- Require negative films to transfer the image.
- Standard plate processing steps include exposure through the film, washout, drying, finisher.
- Higher production times and costs due to film requirements.
- Offer tried and true process familiar to most printers.
Digital Plates:
- Replace traditional film with digital laser etching of the image onto the plate.
- Eliminates the lead time and costs of film output.
- Enables a more streamlined platemaking process.
- Provides consistency and quality on par with offset and gravure.
Laser-Engraved Plates:
- Originals are engraved directly onto the plate using fiber or CO2 lasers.
- The non-photosensitive material often contains light-absorbing additives to optimize engraving.
- No chemical processing required.
- Enables precise, clean image reproduction.
- Leading manufacturers include Continental and Böttcher.
Plate Thickness Classifications
Thick plates (3.94mm+):
- Highly elastic thick plates withstand pressure fluctuations on uneven or irregular substrates.
- Well-suited for corrugated cardboard, tissue, and other packaging applications.
- Limitations include slower printing speeds and excessive dot gain.
Thin plates (0.76mm to 2.28mm):
- More dimensionally stable and rigid than thick plates.
- Enable superior ink transfer and fine halftone dots.
- Ideal for labels, folding cartons, flexible packaging.
- Thinner 1.14mm plates commonly used for varnishing and coating.
Development Method Classifications
Solvent-Wash:
- Solvents remove unexposed polymer portions during development.
- High productivity and workflow compatibility.
- Environmental considerations of solvent disposal.
Water-Wash:
- Aqueous solutions used for developing, reducing environmental impact.
- Limited by slower washout speeds.
- Leading manufacturers include Asahi and Toyobo.
Thermal:
- Exposure to heat activates the resin and removes unexposed areas.
- No chemical processing required.
- Speed and quality still developing.
Laser-Engraved:
- No chemical or water washing needed, only debris removal.
- Very streamlined environmental process.
- Precision imaging control.
Key Terminology
- Round-Top vs. Flat-Top: Refers to dot shape and profile.
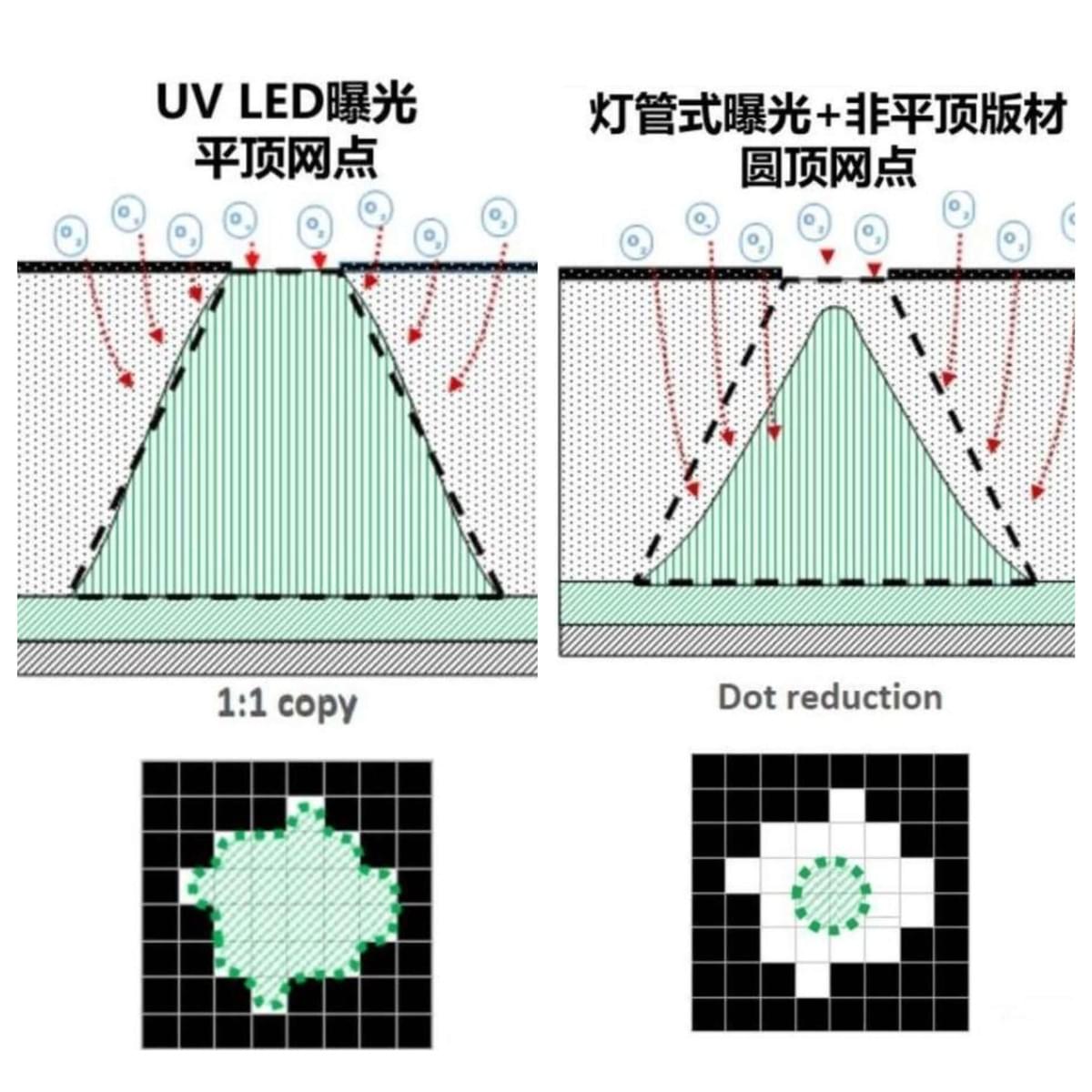
- Smooth vs. Sand-grain(Dull-polish): Mostly flat-top plates. Sand-grain plates have enhanced ink transfer properties, making them suitable for film printing.
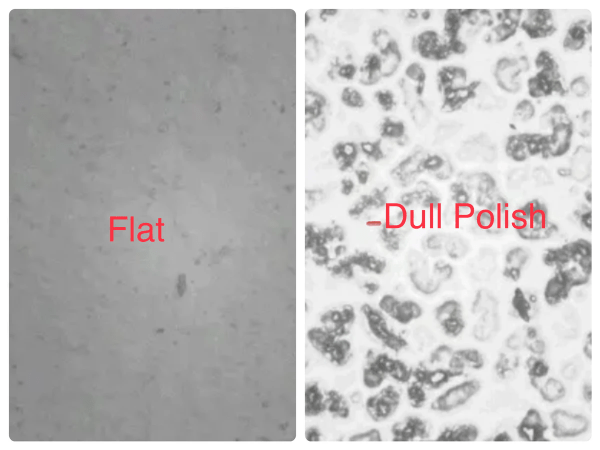
- Digital: From image digitization, not plate material
The wide range of flexographic printing plates available today provides printers with options suited for virtually any substrate and application. By understanding the core classifications of plates based on photosensitivity, production process, thickness, and development method, flexo printers can determine the optimal plates for their specific print needs. Likewise, being aware of the latest plate technologies and terminology enables educated discussions with plate vendors and suppliers. This guide provides a deep dive into the world of flexo plates in 2023 to deliver the knowledge printers need to elevate their flexo operations.